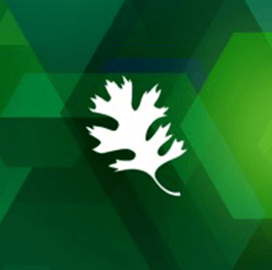
Record-breaking results
DOE Laboratory Partners With Airtech for Composite 3D Printing
The Department of Energy’s Oak Ridge National Laboratory has partnered with Airtech International to demonstrate recycling’s potential in reinforcing the composites supply chain vital to advancing 3D printing or additive manufacturing.
According to ORNL, its joint research team with Airtech developed a 3D-printed, large-format additively manufactured mold for the aerodynamic splitter of a race car entered in the 2023 Pikes Peak International Hill Climb. The team recovered hard-to-recycle thermoplastic material to create a new splitter that contributed to the race car’s record-breaking performance in the event, ORNL said.
The ORNL-Airlift team’s mold brought the world’s first fully recycled, 3D-printed, LFAM aerodynamic splitter at lesser cost and reduced environmental impact, the laboratory added.
According to Vlastimil Kunc, the laboratory’s section leader for composites science and technology, ORNL holds the only facilities in the U.S. capable of formulating, creating, printing and recycling composite materials.
ORNL is also working with NASA on 3D printing to create materials for extreme environments. One initiative comes in the form of a 3D-printed wheel made of nickel-based alloy for a lunar rover that the agency plans for a moon landing in 2024.
Another ORNL effort produced a 3D-printed thermal protection shield for a space capsule developed by the University of Kentucky for an entry technology test included in a supply mission to the International Space Station. The test was the first time a capsule with an additively made TPS was launched into space, the ORNL noted.
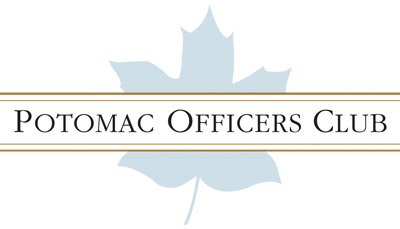
Category: Future Trends